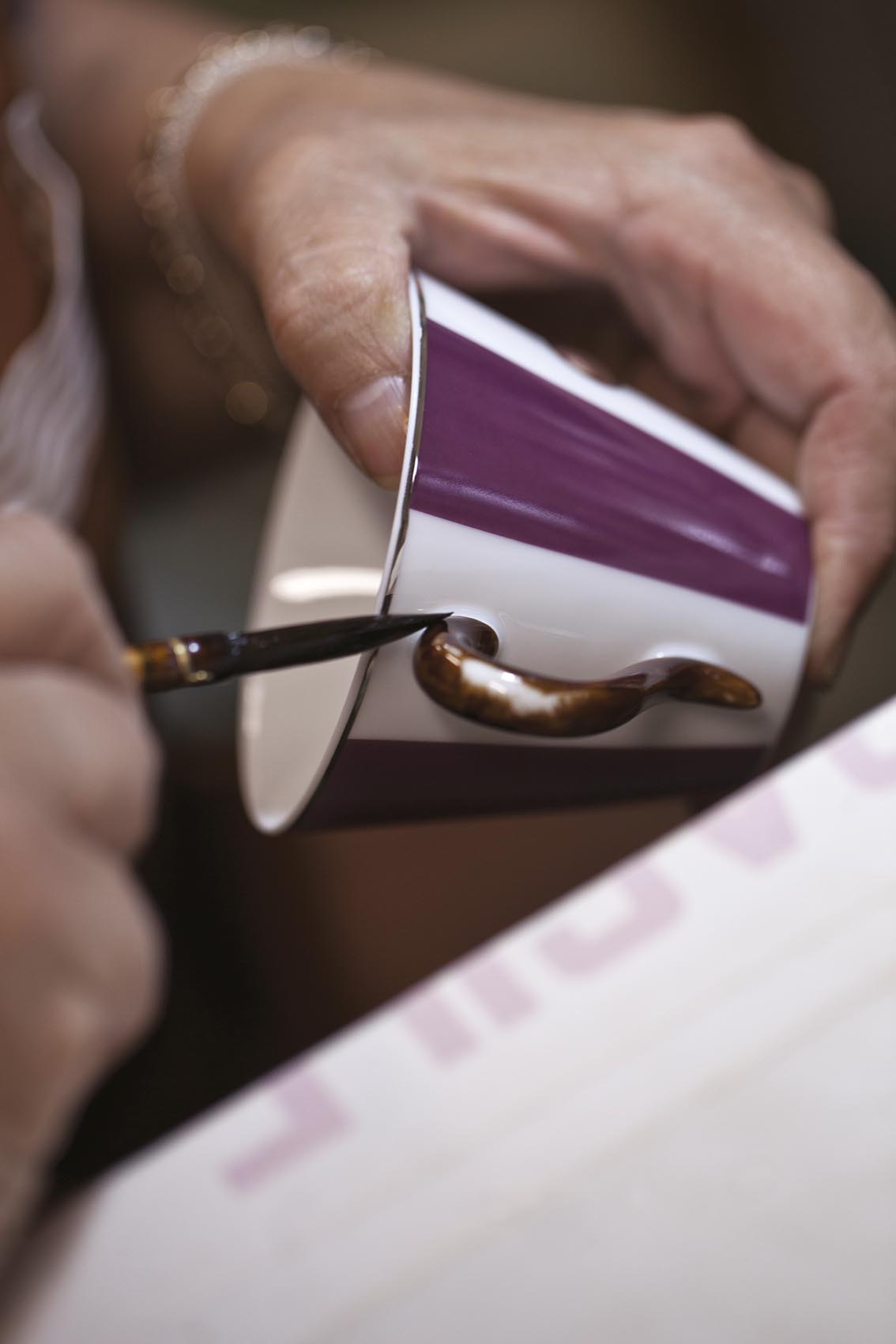
Depuis plus de 150 ans, Bernardaud fait vivre un savoir-faire en le perpétuant et en le diversifiant. Installée à Limoges en raison de la présence de kaolin dans la région (alors utilisé pour blanchir le linge), la Manufacture importe aujourd’hui cette argile blanche indispensable à la fabrication de la porcelaine, mais veille à la sauvegarde de son patrimoine, sans cesser de réinventer les Arts de la table. Visite guidée dans les ateliers de Limoges.
Photos : Bernardaud
« Même si elle est utilisée depuis des millénaires, la porcelaine recèle des propriétés et des applications inexplorées. Pour les révéler, j’ai la chance de pouvoir m’appuyer sur le legs de mes prédécesseurs, cette double richesse qui est la signature de notre maison : le respect des savoir-faire et une recherche de l’innovation faisant fi des conservatismes »
Michel Bernardaud
Le groupe Bernardaud, fondé en 1863, est le premier fabricant de porcelaine de table – il produit quatre millions de pièces par an – en France. Depuis 1986, il intègre l’ancienne Manufacture royale, qui réédite, à l’identique, des pièces de musée des XVIIIe et XIXe siècles. Il collabore également avec des chefs étoilés (Joël Robuchon, Alain Ducasse, Alain Passard, Thierry Marx, Guy Savoy, Jean-François Piège, Helène Darroze …), des designers et des artistes (Christophe Pillet, Andrea Branzi, Hervé Van Der Straeten, India Mahdavi, les frères Campana, Sarah Lavoine, David Lynch, Jeff Koons, Bernard Buffet, Alexander Calder…) qui explorent de nouveaux territoires et s’interrogent sur les nouveaux usages de la porcelaine. Bernardaud l’invite ainsi dans tous les espaces de la maison à travers objets, meubles, et luminaires, investit le territoire plus intime du corps avec des collections de bijoux, réinvente les Arts de la table avec des grands chefs du monde entier, et fait découvrir les créations d’artistes contemporains via des expositions organisées par la Fondation Bernardaud. La première collaboration de Bernardaud avec un designer remonte à 1967. Raymond Loewy dont la devise était « la laideur se vend mal » créa Ariès, un service à l’esprit géométrique, aux lignes pures et d’un blanc uni qui révolutionna le monde de la porcelaine de Limoges et amorça un véritable tournant créatif au sein de la Manufacture.
La table constitue le territoire d’expression originel de la porcelaine. Outre sa blancheur, sa translucidité et sa sonorité délicate, elle est perméable, dure, résistante et conserve sa solidité même à des températures extrêmes. On l’apprécie aussi pour sa pérennité qui demeure sa qualité la plus extraordinaire puisque la porcelaine ne craint ni l’air, ni l’eau, ni le temps. La Manufacture équipe 80% des étoilés Michelin, mais aussi des brasseries, bistrots, restaurants de charme et établissements hôteliers partout dans le monde. Les chefs peuvent demander des décors sur mesure en résonance avec leur lieu ou faire créer de nouvelles formes. C’est ainsi que Bernardaud réalise des commandes spéciales pour des hôtels et restaurants prestigieux (comme la Mamounia à Marrakech), des particuliers, des chefs d’Etat et des entreprises.
L’intelligence de la main
Labellisée « Entreprise du Patrimoine Vivant », la Manufacture Bernardaud propose une porcelaine qui s’affiche à la fois comme un artisanat, une industrie et un art. Dans ses deux sites de production situés à Limoges (le site historique) et Oradour sur Glane (usine d’un hectare occupée à partir de 1979), la main côtoie la machine. Un objet en porcelaine est la somme d’une multitude de compétences, de métiers où règne l’intelligence de la main. Du modeleur au coloriste, en passant par le finisseur ou la décalqueuse, chaque artisan dessine, modèle, émaille, assemble, décore, vérifie, choisie… avec ses mains. Si le toucher et la vue demeurent les sens les plus sollicités, l’ouïe l’est également pour repérer à l’oreille en faisant tinter la porcelaine lors de l’étape du choisissage, d’éventuels défauts comme les fêlures, en particulier dans les tasses. Chaque artisan consacre près d’un quart de son temps à vérifier que chaque pièce est conforme aux critères de qualité définis par Bernardaud. Une mission d’autant plus importante que la perfection de son geste dépend du geste précédent et conditionne le suivant. La qualité d’une pièce est aussi la somme des temps incompressibles nécessaires à sa fabrication, aux séchages et aux cuissons successives. Une théière par exemple, passera dans plus de cinquante mains aux doigts de fées et mettra une semaine à voir le jour.
Les étapes de fabrication du vase Panarea
Quand nous sommes allés visiter le site de production d’Oradour-sur-Glane, nous avons pu suivre la pose de anses sur des tasses, ainsi que la fabrication du célèbre vase Panarea imaginé par Olivier Gagnère, véritable alchimiste du feu.
Tout commence avec la pâte de porcelaine composée de 50% de kaolin, 25% de quartz et 25% de feldspath (minéral à base de silicate double, d’aluminium, de potassium, de sodium ou de calcium). Ces matières sont délayées dans de l’eau, broyées, mélangées, tamisées puis filtrées, pour prendre la forme de galettes avant d’être transformées, selon les techniques de fabrication, en pâte plus ou moins liquide. La pâte liquide, appelée Barbotine, est utilisée pour le coulage. Désaérée et malaxée sous forme de boudins, la pâte semi-molle est utilisée pour le calibrage. En poudre, obtenue par atomisation pour obtenir d’infimes granules, on l’utilise compressée par pressage isostatique.
Mais en amont, la création d’une pièce débute par la création de son modèle. A partir d’un dessin fourni par l’artiste ou le designer, le modeleur réalise l’objet sous forme d’un volume de plâtre à l’échelle « taille crue », soit 14% plus grand que la taille réelle de la pièce (car il faut anticiper le retrait que prendra la pièce à la cuisson). Chez Bernardaud, le chef modeleur, Maître d’Art et Meilleur Ouvrier de France, a 22 ans d’ancienneté. C’est lui qui modèle les moules mère des pièces fabriquées à la manufacture. Des services de table, aux pièces d’exception, il est le premier à intervenir sur la forme. Entièrement vêtu de blanc, Stéphane Bonneau n’est pas un causeur. Quand nous l’avons rencontré dans un magnifique atelier inondé de lumière, il travaillait sur une nouvelle création des frères Campana. « Modeler est un jeu pour moi. Ce métier m’anime profondément. Il change mon regard, ma personnalité, mon rapport aux autres. Rien ne me trouble en modelant, je suis habité par la matière » explique-t-il. « On travaille avec nos mains, la seule machine que nous utilisons, c’est le tour. Il faut s’armer de patience, avoir l’envie d’apprendre, laisser sa sensibilité s’exprimer dans la matière et puis…avoir le geste comme un don ». Une fois le moule mère créé, il est dupliqué en moules de production en plâtre, en résine ou en acier revêtu de polyuréthane.
Vient ensuite l’étape du coulage. La pâte liquide est versée dans le moule en plâtre du vase Panarea. La porosité du plâtre absorbe l’eau contenue dans la pâte et fixe celle-ci contre les parois du moule. Après un temps de prise précis, proportionnel à la dimension de la pièce, l’excédent de barbotine est rejeté. Le vase est alors démoulé puis séché. Il subit alors un retrait de 3%. Serge, chez Bernardaud depuis l’âge de 17 ans, a appris le métier avec un ancien. Astucieux et amoureux du bel ouvrage, il a fabriqué ses outils et les a formés à sa main : ébauchoirs en buis, lames de scies, lames de corsets d’autrefois trouvés sur des marchés, simples couteaux… « Il faut pas moins de six ans pour maîtriser le coulage. Mais je continue à apprendre, à découvrir, à chercher ».
Vient ensuite l’étape du finissage qui consiste à ôter les coutures provoquées par la division du moule en plusieurs parties et à effacer toute autre imperfection. Nicolas Bastien, responsable de la production explique : « la porcelaine a de la mémoire. A l’heure de la cuisson, les défauts vont ressortir ». Lors de notre visite, Bernardette, 37 ans de maison, était justement en train de finir un vase Panarea. Alors qu’elle le lavait délicatement avec une éponge dans des gestes circulaires bien étudiés, elle nous a expliqué : «Il faut que ce soit lisse, il faut que ce soit beau». C’est elle qui forme les personnes qui arrivent chez Bernadaud.
Ensuite, le vase subit une première cuisson à 980° pendant 24 heures dans un four fonctionnant au gaz naturel. Cette cuisson, dite de dégourdi, durcit la pièce, la déshydrate et la rend poreuse afin que l’émail puisse se fixer en surface. Les pigments sont ensuite préparés (après avoir été choisis et testés au sein du bureau de style en charge des recherches sur les couleurs et la faisabilité) puis l’émail est pulvérisé sur le vase à l’aide d’un pistolet. Les parties qui vont être décorées à la main sont protégées. D’autres pièces comme les assiettes sont trempées à la main dans un bain d’émail. Les objets qui ne sont pas émaillés conservent un aspect mat et sont appelés biscuits. L’émail se compose des mêmes ingrédients que ceux de la pâte de porcelaine, mais dans des proportions différentes. L’émaillage est une gestuelle très élaborée qui permet de déposer sur la surface une épaisseur aussi constante que possible. Frank, 27 ans de maison, explique que « la couche d’émail doit être la même partout. Cela nécessite des années de pratique ».
Le vase subit alors l’étape du tri avant de partir à Limoges pour être décoré. Chaque pièce qui sort du four est vérifiée à la main dans « l’atelier de choisissage ». « Certains défauts sont réparables, nous explique Nicolas, mais plus de 25% de la production est écartée lors de cette étape, malgré de nombreux contrôles intermédiaires ». Les défauts les plus courants sont les taches, les fêlures, les manques d’émail, les déformations et fentes.
La décoration
A Limoges, siège historique de la manufacture où sont installés les ateliers de décoration, le vase Panarea est pris en charge par un fileur qui applique l’or au pinceau dans les cabochons.
Le fileur, pose également les filets d’or ou de platine sur les bords des assiettes, les anses des tasses ou les becs des théières, à main levée, à l’aide d’une grande variété de pinceaux.
Le vase subit alors une deuxième cuisson à 780° qui révèle la couleur dorée et mate des cabochons. Ultime étape : le sablage. L’or est frotté avec un chiffon et du sable pour prendre tout son éclat.
Le vase passe alors le contrôle qualité, puis il est emballé.
Nous avons observé d’autres techniques de décoration lors de notre visite comme le décor à la feuille (principe de décalcomanie) apposé à la main. Ces décors sont fabriqués dans l’imprimerie de Bernardaud, seule manufacture de porcelaine à en posséder une, puis installés à la pince à épiler par des ouvrières. L’incrustation est un autre procédé de décor par gravure à l’acide.
Une Fondation d’entreprise au service de la créativité
La visite se termine par le parcours-découverte ouvert au public, qui permet de comprendre les secrets de la porcelaine, son histoire et sa fabrication. C’est l’oeuvre de la Fondation Bernardaud créée en 2003 par Michel Bernardaud qui joue ici un rôle pédagogique. Dans une mise en scène signée Yves Taralon, les créations sont présentées dans des fours, sur des planches en bois utilisées depuis la nuit des temps pour déposer les pièces après chaque étape de fabrication. Une odeur de bois est d’ailleurs très présente ici et on peut toucher les pièces et les outils, mettre en quelque sorte la main à la pâte.. En fin de parcours, l’exposition « My Blue China » apporte un nouvel éclairage sur la porcelaine en réunissant les oeuvres de 12 artistes contemporains, témoignant de l’activité vibrante de la céramique.
L’innovation comme moteur de création
A Limoges, en observant la fabrication de Balloon Dog by Jeff Koons et celle du service Les poissons d’or de Jacques Bernardaud (une réédition qui n’a pas pris une ride), on a mesuré à quel point la préservation des savoir-faire rime toujours avec innovation.
Léonard Bernardaud qui a acheté l’entreprise en 1900 avait misé sur la démocratisation des arts de la table. Ses fils, Jacques et Michel, améliorèrent la production avec un four tunnel alimenté au gaz de ville diffusant une chaleur constante. Aujourd’hui, Michel Bernardaud, représentant de la cinquième génération, poursuit le travail de ses aînés. « Même si elle est utilisée depuis des millénaires, la porcelaine recèle des propriétés et des applications inexplorées. Pour les révéler, j’ai la chance de pouvoir m’appuyer sur le legs de mes prédécesseurs, cette double richesse qui est la signature de notre maison : le respect des savoir-faire et une recherche de l’innovation faisant fi des conservatismes ». Chaque année, Bernardaud lance une douzaine de décors et de nombreuses nouvelles formes. C’est ainsi que la manufacture travaille sur une collection de pots pour l’industrie cosmétique. Fidèle à son histoire, Bernardaud fait confiance à ses intuitions, affirme ses choix et revendique ses coups de coeur.
Bernardaud chez Fenêtre sur cour